Spanning the 3rd Revolution
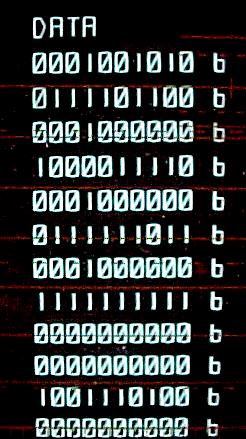
The 3rd revolution is better known as the "Digital" revolution
In this chapter we are going to examine the gulf between the Industrial and the digital revolution, and how the Group handled their transformation because of it. The first revolution was mankind's harnessing of agriculture. The move from a primarily agricultural society to a society that embraced machinery and automation, which replaced much of handcrafted products and goods offered before, was the second revolution. The third is the digital revolution. This ushered in what has become known as the information age. The roots of this phase actually started back towards the later part of the 19th century but did not reach critical mass until the invention of the transistor, and then the integrated circuit. The Grass Valley Group came into being right as the transistor was making major inroads into electronic circuitry. Because of Dr. Hare and Bill Rorden's early mastery of the transistor, the Grass Valley Group never offered a product that used vacuum tubes. Another electronic juggernaut, that made the same early commitment to solid state electronics was Sony, which entered the United States shortly after the Group got started.
Vertical Integration
Even though the Group was now under new management it continued its rise in the ranks of the high end television production equipment industry. This rise manifested itself by the number of employees and real estate the company occupied. While today some companies can grow financially large with few added employees, witness the web economy, back in the 60s and 70s that usually was not even a remote possibility. To grow a company like Grass Valley, they needed to put more people to work to produce more product as sales increased. Either by contracting some of the work out to others, or by hiring people to do the work "in house." Grass Valley evolved using the second approach. It was a highly Vertical Integrated company as it handled almost all of its required stages of production. Early on it even handled all of its own sales and marketing.
It made sense that the Group took this approach when it did, for a number of reasons. One reason was timing. When the company started in the electronic manufacturing business the equipment itself, and the components that made up that equipment were much simpler to create and assemble. A basic machine shop, some assembly stations, or a rudimentary assembly line where circuit boards could be stuffed with parts and soldered, and installed in a case or enclosure, and finally some test equipment to make sure the assembled product was working correctly.
When the Group first started shipping product they did not even have to manufacture or etch circuit boards. As mentioned earlier they used boards that had rows of continuous traces that they would manually cut to organize the components into the required circuits. None of the electronic components back then had any complex mounting requirements. Frames and enclosures where constructed using sheet metal, steel ribbing, and tubing. This approach to enclosures and cases actually continued into the 90s at the company long after circuit boards and control panels had evolved to be quite complex.
Another reason why many smaller companies that grew up around the Grass Valley Group are still very vertically integrated is that they manufacture what is referred to as "low volume, high mix." Historically equipment aimed at broadcasters and other users of high end television equipment was quite expensive. As such it had a limited market. Also most of the gear these folks buy are not stand alone pieces of gear, as a camera or microphone might be, but they are used in conjunction with other equipment that comprise a system.
That system is composed of a mix of gear that is installed to allow the users to perform a specific workflow. That is, a series of tasks performed both sequentially and in parallel to deliver video programming to the viewer. A station that does a lot of news, will have an entirely different workflow than a movie channel. Sports channels will work differently and have people doing different tasks than a channel that does talk shows.
Thus a piece of equipment in this industry usually has to be able to be vastly configurable to meet these varied demands. Often the model X video switcher needs to be produced for one customer that needs 20 video sources fed to it, while another needs 100. As we will see video and audio does not come in one flavor, and today they number more than Baskin-Robbins has flavors of ice cream.
Vertical Integration makes sense when supply chains are not stable, like right after WWII, and before just in time overnight shipping came into being. Transportation is much more robust today. When the Group started roads from all directions into the area were 30 miles of two lane road, through hills and mountains. Even the main road from the town of Grass Valley out to the Bitney Springs site had a one lane bridge. Often large trucks headed to the site had to make a dozen mile detour and approach from the other direction.
So for the first 30 years of its existence vertical integration made sense for the Group. The Grass Valley company today still does much of its own manufacturing, just not in the Grass Valley area anymore, as we will see.
Dan Castles, who was the Groups president in the mid-90s said that when he got involved with the company it looked like a postwar company, as it was heavily vertically integrated. The first time Dan drove up highway 49 in the mid-80s he could not believe a 1000 person company could be up in that part of the world. Dan was the VP of Tektronix's Video Division. At the time the Group had 1200 people working for it worldwide, 900 in grass Valley.
Printed circuit board layout - before computers and CAD
More art than engineering
An eye for detail and a steady hand
Being an outpost in the Sierra foothills, the Grass Valley Group evolved doing as much as possible for themselves. From printed circuit board fabrication (PCB), stuffing parts into those PCBs, machining frames and panels, to testing the final product, originally the Group did it all.
Early on, the Group took raw material and parts in, and through machining, etching, and assembly produced finished products for sale. As we have mentioned, at the volumes we are talking it would not have been very economical to job any of that out in the early years of the company. At one time the Group had about 100 people working multiple shifts in its machine shop. Switcher control panels had hundreds of cutouts, mostly done by hand, for all the switches and other controls that would end up in them.
GVG Machine Shop employees, day and night shifts
Machining hardware into finished products was a multi-step process. Raw metal stock generally arrived as sheet metal or metal bars that underwent the process of being formed into the desired part by a lathe or a milling machine, or both. Drilling operations were common on many parts. Both the milling and lathe processes are similar, but the simple explanation is that with a lathe the part being shaped is rotated while the cutting tool is stationary. With a milling machine the piece being worked on is stationary while the cutting tool rotates. Often individual parts were then manually de-burred, welded to other parts to make a larger assembly, sanded, and then painted or etched/anodized.
Anodizing is an electrochemical process that converts a metal surface into a durable, corrosion-resistant, anodic oxide finish. Aluminum is ideally suited to anodizing, although other nonferrous metals, such as magnesium and titanium, also can be anodized.
Even back then not everything was done in house. Any parts that needed to be painted were sent to outside vendors. Raw sheet metal, which generally formed the outer enclosure needed to undergo punch, bending, additional shearing, drill and tap operations. In addition these parts would often undergo etch/anodizing or nickel plate processes. Nickel plating provided a combination of corrosion and wear resistance. It can add brightness, and luster. It also adds adhesion properties for subsequent coating layers, which is why nickel is often used as an 'under coat' for other coatings, such as chromium.
So the Group, by the 80s was doing almost all of its own machining, and thus most non-off-the-shelf parts where created up on a ridge northwest of town, that is the Bitney Springs site. When you make your own parts you not only have to worry about keeping the assembly line stocked, but also need to create replacement parts for product already out in the field. As such the Group divided the parts they used into three categories with the highest grade, parts that had some cosmetic appeal, such as operator panels, were individually packaged in foam. The next level parts were individually wrapped, and the lowest level might be packaged in paper and plastic, and simply piled together in a parts bin.
The Group in the early 80s went from assembly lines where a single installer might install all the components on a particular board, or completely assemble the enclosure for a product, to what they called flow Lines. Here each assembler only installs a couple dozen components, and it then moves on to the next assembler. The Group hired an assembly engineer, Larry Hoy, to implement that. The company invested in machines that pre-bent and cut leads for the components that were now just dropped into holes in the circuit board by assemblers. This led to higher productivity, but for the person doing the assembly the task became repetitive and there was a loss of pride as a complete assembled board was not a particular assembler's anymore.
Flow line assembly, where parts are "stuffed" into circuit boards, wave soldered, and then those boards are cleaned of all the solder resin residue.
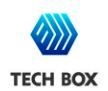
Printed circuit boards
The PCB operations grew to a point that in early 1982 the mother company, Tektronix, gave the Group an order for 3,200 PCBs for a new product line being launched up in Oregon.
To build a complete system you must wire all the sub-components together. Hence the building of wire harnesses. The flow line concept was helpful when it came to constructing harnesses, the bundles of cables that interconnect circuit boards, connector panels and control panels. The ones in a video switcher could take 180 hours to build. If a single installer built the entire harness, by the time they were done the person might have forgotten the initial steps.
Finally you need to be able to test and configure the final product
As we will see later on, as the company continued to change hands, and merged with operations from other companies, some that made competing products, the Grass Valley and Nevada City engineering and manufacturing fortress began to lose out to others spread around the globe. That was not always the case. Shortly after the Group was acquired the third time, by French electronic giant Thomson, a television router division they had in Salt Lake City was brought to Grass Valley. But in later years the bulk of the work migrated away from the area. By 2015, and with the fifth acquisition, this time Belden Cable, the last of the manufacturing was moved to Montreal. We will see later how this saga played out as owner after owner applied successive management philosophies.
But just as Thomson had their Salt Lake City router operations moved to Grass Valley, they also tried to have as much as possible made in Vietnam. The problem is this is only economical if you make many of something, not a few, like Grass Valley was doing. If you are building offshore a few Engineering Change Orders (ECO) that crop up can throw any savings right out the window.
The thought here is that many manufactured goods come out of China today, and since Vietnam is a neighbor, although neither are friendly to each other today, the same cost savings might be had. There are a couple reasons this did not work. One we already mentioned. But the other difference is that the Chinese have the infrastructure to iterate many times until they get a manufacturing sample and then copy it millions of times. Hard design is a small part of that process. Again, you cannot afford this in low volume/high mix manufacturing.
While process is important in any set of steps to take raw parts and materials and turn it into a finished shippable product, the task gets much more intricate as more of the finished product is siloed together. Birney Dayton, who had a number of hats at the Group, director of engineering was one of them, and later spearheaded the Groups only real spin off, NVISION, was an early apostle of process, and the aspect of who was responsible for it every step along the way.
Complicated electronic equipment, which is what most of the Group's products were, created many opportunities to get things wrong in their design and construction. Not only did the engineers need to create solid, stable, and robust designs, in both hardware (PCBs, frames, control panels) and the software that even back then drove much of the hardware, but then manufacturing has to be able to replicate the design and see that it is built so that one example of a product is indicative of all the others like it.
At each juncture, the chance for missteps is many. It starts right after the design phase. Even if the engineer nails the circuitry needed to accomplish a given function, how is that design, usually in the form of a schematic, conveyed to the people who need to document the design. While considered quaint today, schematics and other parts diagrams used to be considered a required ancillary part of any product package. Thirty years ago schematics were considered essential as most professional television facilities expected to be able to repair the equipment they bought.
At one time technicians at a facility were expected to troubleshoot problems down to a particular component on a board and replace it. Over time PCBs became so intricate that they could not be repaired in the field as the owners of that equipment could not justify investing in the expensive equipment necessary to accomplish that. So troubleshooting was just to determine which PCB was defective. Today many product's parts and subsystems are so intertwined and constructed as to not allow anyone but the manufacturer or authorized repair agent to successfully deconstruct, repair, and re-assemble a broken product.
So even though schematics are useless now to the end user, they are still vital to the manufacturer. Just as the product has become too perplexing for outsiders to cope with, it has become increasingly complicated for those who build them. So back to the schematic. The blueprint of the designer's solution. It is a collection of data points that must be managed and tracked. The manufacturing engineer must control each piece of data, that there is one point of entry, one master record. They must control who can change that record or piece of data. Inevitably new designs will have lots of changes as problems crop up in produced products, and they are corrected. In the 80s, before software like AutoCAD became ubiquitous, schematics were usually drawn by drafters. The engineer would hand draw their circuits, pass them off to the drafter, who would return the "formal" schematic to the engineer for sign off.
Today, with all the advance design software available engineering will create the schematic, it won't be scratched on a piece of paper and handed off to a drafter. Today the schematic capture tool has the parts data in it and creates a Bill Of Material (BOM). No human hand actually touches the BOM. It has hooks to add mechanical pieces to the board. Now PCB layout software adds location and orientation data. If the layout software catches potential errors: such as traces that are too long, or the need for more capacitors, engineering has to correct that, not someone else. Today only the original engineer should touch the schematic.
The manufacturing department programs the pick and place machines, which includes the order of assembly. Big parts might be found to be in the way of small parts. Again new data, that must become part of the same master record. An important part of the auditing in this manufacturing system is who owns each data entry in the record. Mistakes happen when many can change a record and thus no one owns that piece of data. Errors can quickly creep in.
While greatly automated today as you can see, imagine in the 80s when the process lived on paper schematics and checklists, and not in database records as they do today. What automation was available then lived as islands of data, and not networked together so one database can control the whole process.
Today the biggest hurdle is that the folks overseeing the corporate IT structure often insist on being the overlords for the process and manufacturing engineers that are held responsible for the final result.
A big goal for a company is to have as many early examples as possible of a product be fixable enough to be salable. In the 80s that might mean only 50% of first run boards. Today it is expected to be near 100%.
In addition, as we have mentioned, the Group, as with many other vendors of high end video equipment, both in the area and worldwide, must be able to cope with low volume, high mix products. When you were doing low volume, and high mix you need your own manufacturing, otherwise it is too expensive. This means those companies need an economic manufacturing quantity of one. They need to make one of something and make money at the same time. This is accomplished by arranging their manufacturing line to a place where changes to the line for a different product, besides maybe changing out a parts wheel, is as little a task as possible.
As we will see shortly through the 80s and into the 90s the vertical integration process worked fairly well for the Group. But not always.
Hence: You need a facility that was known as Bitney Springs!
Bitney Springs
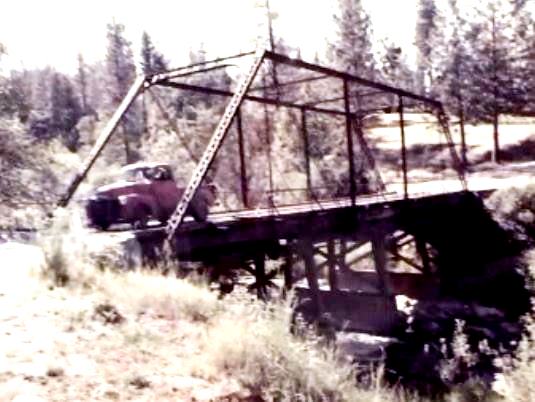
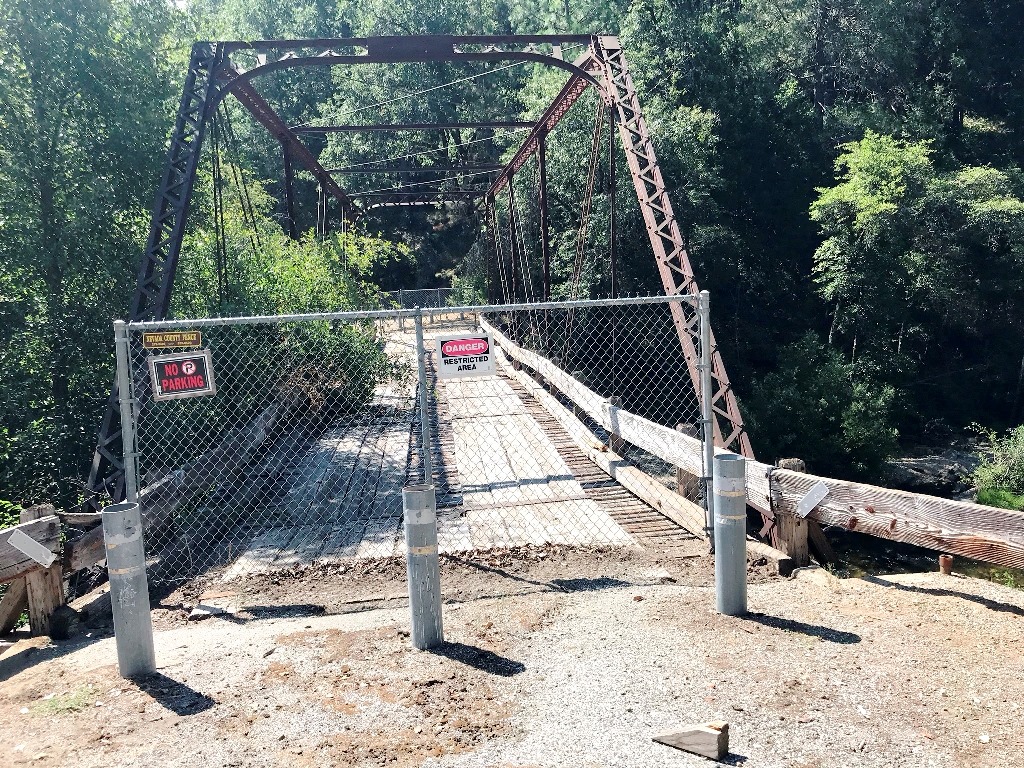
Originally the main path from Grass Valley to the site required crossing a one lane bridge!
While the Bitney Springs site would not make much sense today, it made sense when the Group did most things itself.
As discussed earlier Hare bought 80 acres of property he had discovered back in the early 60s. It had a good view of the Sacramento Valley, and it was at an altitude that allowed it to be above the winter tule fog layer that sometimes hung over the valley. A previous owner apparently had planned some development on the land and had leveled an area that was perfect for a building pad.
As also mentioned earlier Hare got a deal on the property because he put out word that the property he had already obtained was to be used as a chicken ranch. Some wondered if Hare had got the idea to claim that because after Hare and Litton had their falling out, Hare quickly set up shop in what was an abandoned chicken processing plant.
Originally the area only had single-phase power, and after fighting with the power company the required conductor was added so that the site had three-phase power. The site had natural spring water and the company built a water tank on high ground to store the water and provide adequate water pressure and created a couple ponds.
The Bitney Springs site always faced a fire danger, and Hare had stated that if there was ever a fire that came through and took out the trees that he would have to move as he would not be able to stand the desolation. What did not help was that the site had Manzanita which burns very hot and is difficult to extinguish. They kept a gasoline powered pump with attached water hose near the lake and the main building. The company's maintenance crew regularly cleared fire lanes to minimize the spread of fire. They created a second pond to increase the amount of water available to fight a fire.
So besides the original building one, a A-frame house for the Hare's on Kentucky ridge overlooking the site and Deer Creek to the south, and a guest house, were the original structures on the property. Eventually the guest house was consumed by fire.
Building one was everything at first; administrative, modular test and development, Dr. Hare's office, and even early routers.
Growth was thus that three more buildings were added in 1969. The site had grown to 120 acres set amongst the trees and it looked more like a college campus than an industrial park. A lot of this growth was from the sale of video switchers, which then comprised over half of the company's sales.
As the 60s wore on, more television stations were specifying Grass Valley gear sprinkled in with RCA, GE, and other large vendors when equipping a station. The volume of product being sold and produced had increased to a point where the Group needed to consider building a second building. Since Hare did not want to take trees out of the current property, he put an option on an adjacent property that was an open field, once used for cattle grazing. By the end of the year the Group owned that property and promptly set out to create a building identical to the first, mainly to save time as orders were increasing and lead times were getting longer. Building two became everything switchers. Eventually building two was the model shop for prototypes and technical arts (manual publication).
Building three was manufacturing, the machine shop, PCB fab, & assembly. The building had two wings; one was PCB fab, and they had to re-pour the concrete floor in that wing of the building after PCB operations moved out. The other wing of the building was where the machine shop was. Later when the machine shop moved to building nine the wing became manufacturing. CAD (design) was also in that wing, which at the time was composed of Intergraph graphics terminals and a VAX central computer. This was long before the advent of the PC and Sun and Silicon Graphic workstations. Later Intergraph played a larger role in the Grass Valley story.
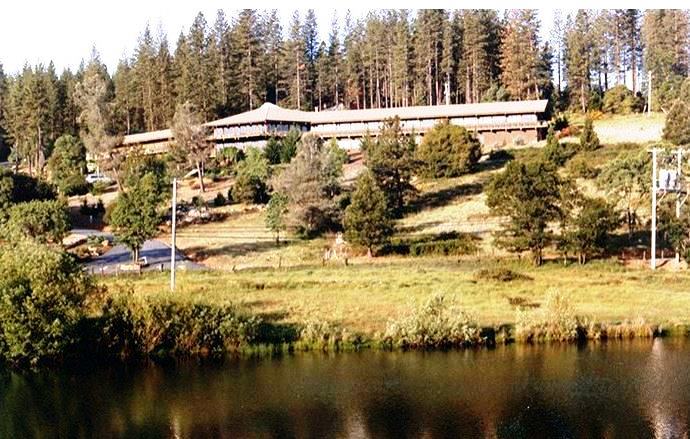
Building 4 1977
In 1976 building four was built. Production switchers and routers moved to that building. It was the stateliest building on the campus and was the center of gravity for the campus for a long time. It made a great initial statement as you drove up through the main entrance. Sadly today it is closed and not used by the current site occupants due to internal mold issues.
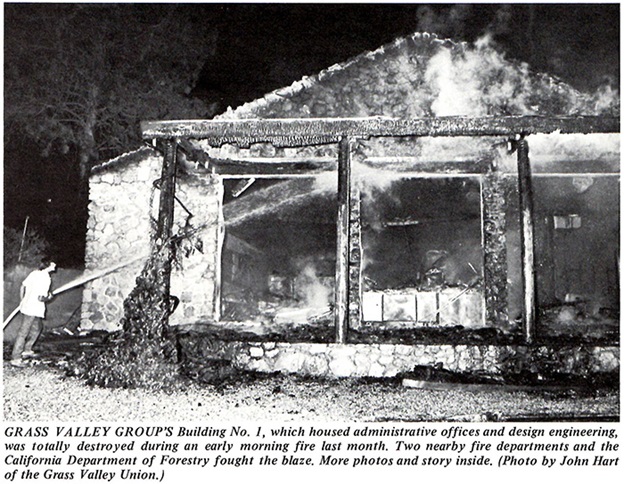
Building 1 fire
Trade magazine account
Building five was built in a hurry after building one burnt down on August 1st, 1977. Buildings 5, 6, and 7 were all metal buildings.
What was in building one was moved initially into Dr. Hare's house, then into building 7 when it was completed. Building 7 was thrown together and used shredded paper infused with boric acid, to fireproof it, they put some glue into it and sprayed it on the inside of the metal building to insulate it. Heat in the building were open radiators not vented to the outside. Company engineer Jim Michener walked in, looked up and said, "you know it's going to rain in here." The gas heaters produced water vapor that condensed in the insulation. He was right, it did rain in the building on occasion. Building 7 and 8 both had heating issues over the years. Early video routers were assembled in building 7. Eventually building 8 housed the executive offices.
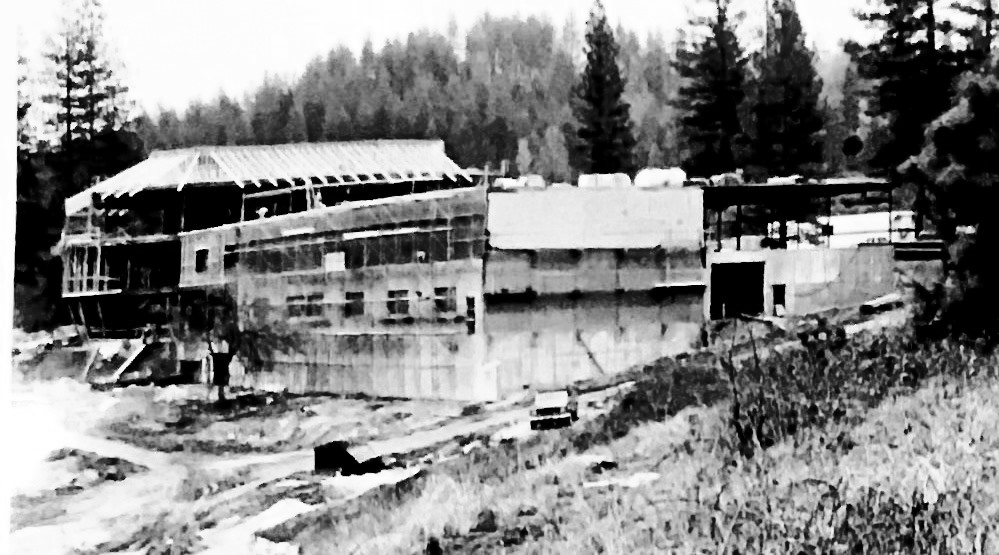
Building Nine under construction
Building 9 was next after 8, actually 8 and 9 were practically built concurrently. Building 9 was started in 1979. But it was not finished until the beginning of 81 due to an electrician's strike. The building was the sites largest at 76,500 sq ft. PCB fab moved to building 9 first. Switchers and routers moved into 9. Eventually the building also hosted systems assembly and test, modular assembly and test, the machine shop, production control, and admin. The building at one time hosted more than 400. Up until this time switcher control panels were manually cut out with a template and finished by hand. With the move into 9 CNC was introduced to speed up switcher panel construction. The building was the first with its own backup power and had a fairly elaborate HVAC system controlled by pneumatic solenoids.
Sadly as operations started winding down at the site this building was one of the first to empty out.
The machine shop held out until the 90s when it was sold off. The company that bought the machine shop ended up buying the entire Bitney Springs site. Chuck Conners was running it. Metals at some point just became a tough commodity to be in.
The last Bitney Springs building: Nine
The building also hosted a number of company operations: Admin, PCB Fab, Machine shop, among others
Also the view from the cafeteria in the building
Beginning of the end
In 1988 there were 1000 people on the Bitney Springs site. There was only one way in from Grass Valley. At the time the Group was producing $30 million of income, on a fire prone ridge.
On the ominous date of Sept. 11, 1988, the idyllic site was no longer that idyllic. A little after 9 a.m. what became known as the 49er Fire started. The name came from the highway. It was started near an abandoned house that was called home by a vet that was down on his luck. It started north of the South Yuba River and was quickly driven to the southwest by gusty winds. By the time it was contained on Sept. 13, it had burned 33,700 acres, 52 square miles, and had destroyed 312 structures, 148 homes (about 15 of those where Group employee homes), 89 vehicles and 17 boats. Approximately 3,200 firefighters, 285 Engines, 65 Dozers, 76 Hand Crews, 12 Air Tankers, and 8 Helicopters worked for more than a month to completely extinguish the fire.
Photo on the right is what's left of one of the GVG out building on the site
At the Bitney Springs site it blackened 150 acres, or about one-half the site, and did $500,000 in damage, which happened to equal the company's deductible. It leveled two small buildings. While it threatened many of the site's buildings, they survived with a pink coating of fire retardant from air drops. The suppression costs were estimated at $7.5 million, and the total losses were estimated at $22.7 million in 30 year old dollars. At the time, the 49er Fire was the 3rd most destructive fire. Today It is not even in the top 20.
The fire did manage to blacken 150 acres, or about one-half the site, and did $500,000 in damage, which happened to equal the company's deductible. It leveled two small buildings. While it threatened many of the site's buildings, they survived with a pink coating of fire retardant from air drops.
The suppression costs were estimated at $7.5 million, and the total losses were estimated at $22.7 million in 30 year old dollars. At the time, the 49er Fire was the 3rd most destructive fire. Today It is not even in the top 20.
The 49er Fire map. Black Dot in center is the Bitney Springs site
The site also became expensive to meet the mounting environmental pressures and restrictions. The need to geographically diversify became apparent.
Besides the fire hazard that existed, the site was situated on land that was considered rural. It was the only industry of any size for many miles in any direction. Nevada County, which is infamous for red tape and fees to make any improvements on properties, was particularly attuned to policing what the Group was doing with the site. Many claim to this day that the county counts on fees and fines on contractors and builders for a sizable chunk of the county's funding. As a result many remodels and additions in the county are done without pulling any permits.
When the Group decided to rebuild building one here is a partial list of the hurdles they had to clear:
- Describe the property as it is now
- Describe the surrounding properties
- Describe any change in terrain
- Any geologic hazards
- Any change in the building footprint on terrain
- Effect on water tables
- Change in air movement, dust, pollutants
- Any deterioration in air quality
- Change in area noise or vibrations
- Changes to flowing or standing water or marshes
- Changes in ground absorption rates and drainage and surface water runoff, ground water currents
- Any change to animal habitat
- Trees affected
- Effect on the nearby community; population, transportation
- Effect on public services
- Effect on energy usage
- Effect on aesthetics and scenic views
- Effect on historical and archaeological sites
- Affect the employment and tax base of the county
Remember, this was not a new building, just a replacement for an existing one. At one time the company actually considered the possibility of employing 2000 on the site. By the early 80s that thought was fading fast. Even before the fire the fact that the vast majority of employees were still crossing a one lane bridge (replaced in 81) and the site was miles away from major highways, started to weigh on the Groups management. Britney Springs site was becoming environmentally difficult to justify.
The fact that the building 9 generator had a couple fuel leaks did not help stem the County's scrutiny of the site.
While the setting was idyllic, looking more like a college campus than the site of the largest manufacturer in the county, it was expensive to maintain. Not only building wise, but the constant upkeep on the 300 plus acres the site came to occupy. The Group also had to maintain their own water supply. The maintenance crew spent a fair amount of time clearing brush to minimize the fire danger.
Most employees liked the campus nested throughout the trees on the side of a gently sloping hillside. Employees would get around the campus via company bicycles. They would walk out of a building and hop on an available bike and pedal to their destination. Kids were hired whose job was to keep the bikes evenly distributed around the campus. As the company's growth slowed and demands to stay profitable rose, these types of perks were becoming hard to justify.
At the time, the area was a desirable place to live, and the Groups turnover rate was less than 15%/year. Up to this point many thought the company's employment growth rate would continue at 15%.
So a change in management philosophy started to set in. Much of it was creeping in via their Tektronix overlords. In a remote, high priced area, which Grass Valley and Nevada City were even then, should you be so vertically integrated, with it all leveraged in one location?
Providence Site
Back in December 1982, the Group bought a second site, 160 acres, which was known as the Providence Mine site, after a mine complex that lied underneath. At the time, the Group was still experiencing rapid growth, and besides some 2000 employees that they once thought possible at Bitney Springs, they planned for this new site to hold an equal number. Yes, in the early 80s the Group envisioned a future with 4000 employees in the area. The new site had a number of advantages. It was 500 feet from a main water line, and adjacent to Nevada City's wastewater plant. It had easy freeway access and was still secluded at the same time, lending itself to the campus-like environment GVG maintained at the Bitney site. Another plus was that when customers came to visit, the new site was much closer to hotels/motels, restaurants, bars, etc.
By 1996 the Bitney Springs site had been emptied out. The total local employment went from almost 1000 at Bitney Springs in the early 80s, to a peak of 1200 in the area in the late 80s, and then started a slow but continuous decline to around 550 at the turn of the century. After a number more purchases by outsiders and emancipations in 2015 the remaining 200 people still employed locally by the company moved into a 41,000 square foot building that was originally owned by the only spinoff the company ever had.
Only four of the nine planned buildings (red) were ever built. One of those four was a guard shack. The blue line depicts the southern portion of the site, which was sold off in 2000.